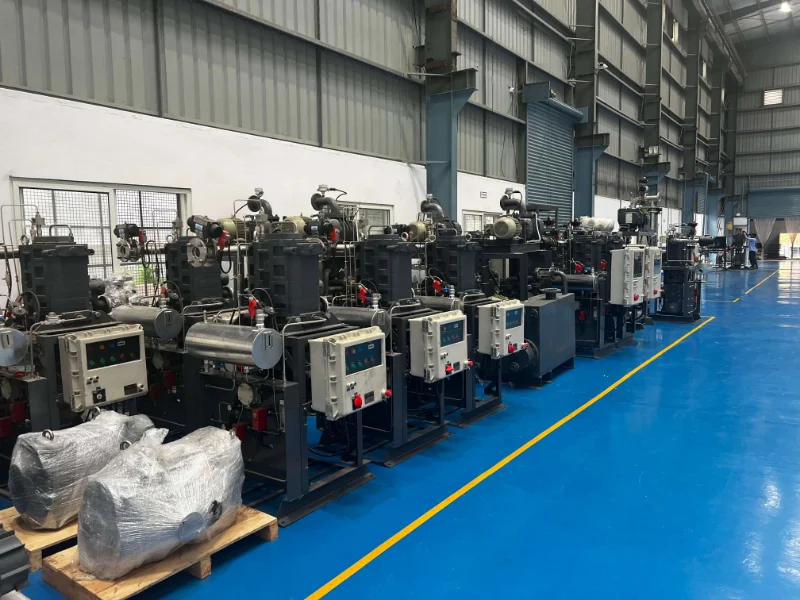
Dry vacuum pumps are prized for their clean operation, low maintenance requirements, and reliability across demanding industrial environments. While they eliminate the need for oil-related upkeep, regular maintenance remains essential to protect your investment and keep operations running smoothly.
At Stanpumps Engineering Industries, we help clients optimise vacuum performance with tailored maintenance programmes that reduce wear, prevent failure, and extend service life. Whether you’re running dry claw, lobe, or booster pumps, the following practices can make all the difference.
Dry vacuum pumps use synchronised rotors that operate without internal lubrication. This design removes the risk of oil contamination and is ideal for applications in pharmaceutical, chemical, and food processing.
Key internal components include:
Although these pumps have fewer moving parts in contact with process media, they still require regular care to maintain efficiency.
Routine visual inspections go a long way in identifying early warning signs. Operators should be trained to observe and document key indicators as part of their standard operating procedures.
Key checks to perform regularly:
Stanpumps recommends integrating these checks into daily or weekly plant routines. Consistent monitoring helps you act before a small issue escalates into system failure.
Though oil-free, dry vacuum pumps still rely on critical filtration systems to protect the pump internals from particulates, vapours, and condensable gases.
Stanpumps Engineering Industries advises:
If operating in high-dust or chemical-rich environments, filter maintenance becomes even more critical.
Most dry vacuum pumps feature air or water cooling to manage internal temperatures. Heat buildup can damage seals, reduce efficiency, and warp metal components.
To ensure cooling systems perform effectively:
For air-cooled systems, verify that ambient operating conditions meet manufacturer guidelines. Excessive room temperature or poor ventilation can compromise performance.
Although dry pumps are highly resistant to contamination, exposure to harsh vapours, corrosive gases, or condensable substances can still cause deposits to build up internally.
Stanpumps Engineering Industries recommends:
Custom accessories, such as inert gas purges or anti-corrosion coatings, can be supplied based on the application.
Even low-maintenance machines need periodic in-depth servicing to ensure continued performance. Stanpumps offers a structured preventative maintenance schedule based on usage intensity and application risk.
Typical service intervals may include:
Service timing can be adjusted for heavy-duty or continuous operations. Stanpumps provides guidance on setting schedules based on real-world usage data and environmental factors.
Modern dry vacuum pumps can be equipped with digital sensors to enable predictive maintenance strategies. This technology tracks:
Stanpumps Engineering Industries supports integration of IoT-enabled systems that allow remote performance tracking and alerts for deviations. This reduces the need for manual checks and enables proactive servicing.
If a pump is not in use for extended periods, proper storage procedures are critical to avoid internal corrosion or damage.
Stanpumps recommends:
Stanpumps can provide detailed storage guidelines or on-site preparation services when equipment is temporarily decommissioned.
Dry vacuum pumps are reliable, durable, and clean by design but proactive care remains key to extracting their full value. With proper maintenance, pumps from Stanpumps Engineering Industries deliver consistent performance for years, even in the toughest industrial environments.
Contact the Stanpumps team today to schedule a maintenance assessment or to learn more about service packages tailored to your operation.