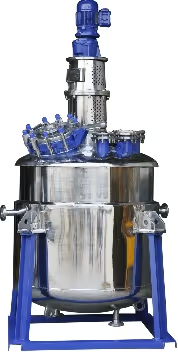
Using solvents in any manufacturing process requires solvent charging, removal and storage. Each stage creates solvent vapours in addition to those that are generated when the solvents are physically used in the manufacturing process. Recovering these solvent vapours is critical for process operational efficiency, plant cost savings, operator health & safety and environmental legislation compliance.
There are many industrial applications which involve the processing of solvents. Such applications include; distillation, drying, evaporation/crystallisation, solvent/vapour recovery and filtration and equipment includes reactors, mixers and dryers. In the Pharmaceutical sector, for example, solvents which are used in the reactors are typically displaced through a vent system to a solvent recovery system and in larger plants, multiple reactor systems often to vent to a common solvent recovery unit.
Some vent systems are “one-pass” systems whereby the vapours are exhausted from the reactor, pass through the recovery unit, are cooled, and expelled to the atmosphere (where applicable). In the reactors, mixing, coating, and drying/granulating operations, a more efficient and economical method of solvent recovery is to use a “closed-loop” system.
A closed-loop system is best suited for batch processing systems, but can also be adapted to a continuous feed system. The closed-loop system has the advantage of having no emissions during operation, which in effect gives a 100% recovery of the solvent. This is very commercially attractive to the manufacturing plant and much safer for operator welfare.
The most common closed-loop system employs a vacuum pump for handling solvents. There are several types of vacuum pumps which could be employed including Liquid Ring, Dry Pumps, Rotary Lobe, Claw and Screw pumps. These systems tend to not require internal lubrication so allows solvent vapors to be sucked through the pumps without jeopardising the lubrication. By contrast, oil sealed pumps such as rotary vane or piston that do require internal lubrication typically have problems on such duties.
Both Liquid Ring and Dry Pumps have external bearings which are isolated from the process fluid. In addition the Dry Pump also has oil lubricated timing gears to maintain the two parallel shafts rotating in the correct phase to avoid contact. Given the variety of options, the user needs to understand the potential issues of each.
For example, screw pumps have a high potential wear rate as they have to operate with very close radial clearances. Stainless steel rotary parts contacting stainless steel stationary parts creates galling issues which can lead to high heat generation and premature pump failure.
Some pump manufacturers help to overcome potential galling contact issues by manufacturing their pumps from ductile cast iron materials. Unfortunately, this opens up another set of issues given condensation, as encountered in solvent recovery applications, is disastrous for pumps which are made of materials which can corrode. Furthermore, as many pumps are horizontally orientated, this condensation can not escape. This results in high corrosion attach of ductile iron material leading to loss of radial clearances and premature pump failure.
Wherever possible, the best approach is a self-draining dry pump design, manufactured from non-galling materials which is mounted in a vertical orientation. This ensures that there is no stagnation of the product media and less chance of condensation between counter-rotating components. As such, one design that has won favour with rotating equipment engineers around the world, is the ADVV - Automated Dry Vertical Vacuum pump from Stanpumps. The Stanpumps ADVV creates an ideal operating environment for 100%, closed loop solvent extraction and recovery, as found in Reactor, Mixing and Drying applications.