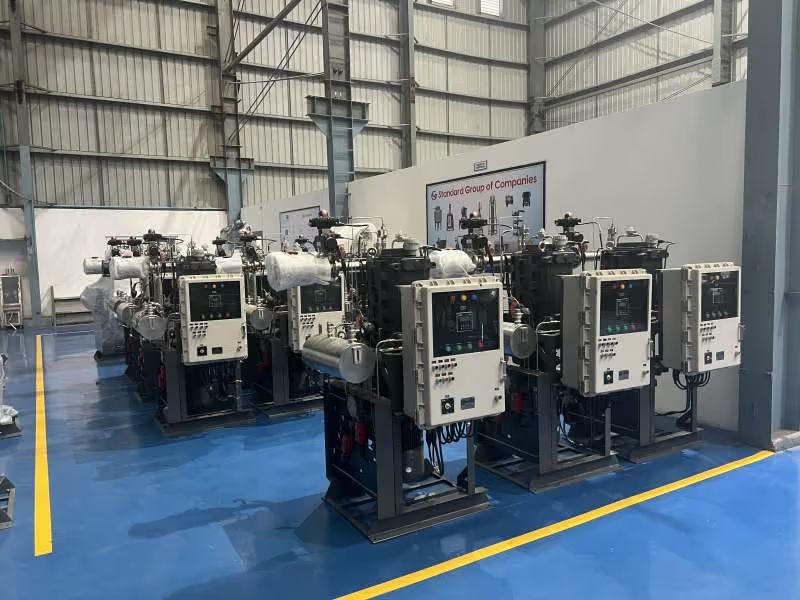
Preventive maintenance is a proactive approach designed to keep vacuum pumps operating efficiently by addressing potential issues before they lead to failures. Unlike reactive maintenance, which focuses on repairing breakdowns, preventive maintenance involves scheduled servicing, inspections, and component replacements to ensure continuous operation.
For industries reliant on vacuum pumps, such as pharmaceuticals, food processing, and semiconductor manufacturing, unexpected downtime can lead to production delays and financial losses. Implementing a structured maintenance strategy helps prevent such disruptions while improving equipment performance.
Unexpected equipment failures can bring production lines to a halt, leading to lost revenue and missed deadlines. Regular preventive maintenance allows for early detection of wear and tear, reducing the risk of sudden breakdowns and ensuring consistent performance.
Vacuum pumps operate under demanding conditions, often handling corrosive gases and high temperatures. Without regular maintenance, internal components can deteriorate, leading to premature failure. Scheduled servicing, including lubrication, filter replacements, and component inspections, helps extend the pump’s operational life.
A well-maintained vacuum pump operates more efficiently, consuming less energy. Issues such as clogged filters, leaks, or worn-out seals can force the pump to work harder, increasing energy consumption. By addressing these problems through preventive maintenance, businesses can reduce electricity costs and improve overall efficiency.
Emergency repairs are often more expensive than routine maintenance. When a vacuum pump fails unexpectedly, businesses may incur high costs for expedited repairs, replacement parts, and operational downtime. Preventive maintenance minimises these expenses by addressing minor issues before they escalate into major failures.
Vacuum pumps play a critical role in various industrial processes, from chemical production to food packaging. Any fluctuations in vacuum pressure or performance inconsistencies can compromise product quality. Preventive maintenance helps maintain stable vacuum levels, ensuring reliable and repeatable results.
Scheduled visual and operational inspections are essential for identifying early signs of wear or damage. Maintenance teams should check for leaks, abnormal noises, and fluctuations in vacuum levels to detect potential problems before they worsen.
Filters and seals play a crucial role in maintaining vacuum pump efficiency. Over time, contaminants can clog filters, reducing airflow and placing strain on the pump. Replacing filters and checking seals for leaks helps maintain optimal performance.
While dry vacuum pumps do not require lubrication, other pump types rely on oil or cooling fluids to prevent overheating and reduce friction. Regularly checking and replacing lubricants ensures smooth operation and prevents component wear.
Leaks in vacuum lines or faulty valves can compromise pump efficiency. Routine testing of connections, hoses, and valves helps prevent vacuum loss and maintains system integrity.
Contaminants such as dust, particles, and chemical residues can accumulate inside the pump, affecting performance. Regular cleaning of internal components and exhaust systems prevents blockages and enhances reliability.
Developing a structured maintenance plan ensures vacuum pumps receive timely servicing, reducing the risk of failure. Key considerations when designing a maintenance schedule include:
In addition to routine servicing, industries are adopting predictive maintenance techniques that use real-time data and condition monitoring to anticipate failures before they occur. Sensors and diagnostic tools measure parameters such as temperature, vibration, and pressure fluctuations, allowing maintenance teams to detect anomalies early.
By integrating predictive maintenance with a structured preventive maintenance plan, businesses can further reduce downtime, optimise service intervals, and enhance overall equipment efficiency.
Pharmaceutical companies rely on vacuum pumps for drug production, sterilisation, and packaging. Unplanned pump failures can disrupt production and lead to contamination risks. Preventive maintenance ensures uninterrupted operations and compliance with stringent industry standards.
Vacuum pumps play a vital role in food preservation, packaging, and freeze-drying. Ensuring pumps remain in optimal condition prevents contamination and maintains product integrity.
In semiconductor fabrication, vacuum pumps are essential for maintaining cleanroom conditions and handling delicate processes. Any variation in vacuum pressure can impact production quality, making maintenance critical for consistent results.
Vacuum pumps are widely used in chemical manufacturing for solvent recovery, distillation, and gas compression. Preventive maintenance reduces the risk of pump failures in corrosive and high-temperature environments.
Selecting a trusted service provider for vacuum pump maintenance ensures expert handling and long-term reliability. Stanpumps Engineering Industries offers tailored maintenance solutions designed to keep vacuum pumps operating at peak efficiency. From routine servicing to advanced diagnostics, our maintenance programmes help businesses reduce downtime and improve operational performance.
Preventive maintenance is essential for minimising vacuum pump downtime, reducing repair costs, and extending equipment lifespan. By implementing a structured maintenance plan, businesses can improve efficiency, maintain consistent performance, and avoid costly disruptions.
Regular inspections, timely component replacements, and advanced predictive maintenance techniques contribute to a reliable and cost-effective vacuum system. For industries that rely on vacuum pumps, investing in preventive maintenance is a strategic decision that ensures long-term success.
Unplanned downtime and costly repairs can disrupt production and impact efficiency. At Stanpumps Engineering Industries, we provide comprehensive preventive maintenance solutions to keep your vacuum pumps running smoothly, efficiently, and reliably.
Our expert maintenance programmes help businesses reduce repair costs, extend equipment lifespan, and ensure consistent vacuum performance across industries such as pharmaceuticals, food processing, semiconductors, and chemical manufacturing. With proactive servicing, routine inspections, and predictive maintenance integration, we help you avoid unexpected failures and optimise system efficiency.
Contact Stanpumps today to schedule a tailored vacuum pump maintenance plan and keep your operations running without interruptions. Let’s work together to ensure long-term reliability and cost savings!