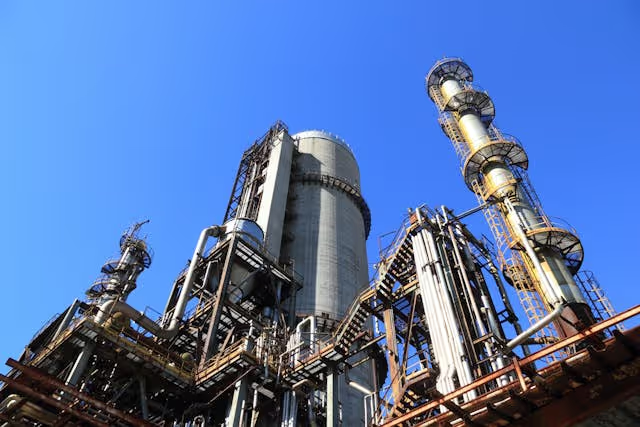
Dry vacuum pump technology is widely adopted across various industries due to its oil-free operation, energy efficiency, and low maintenance requirements. These pumps provide a clean, contamination-free vacuum environment, making them ideal for sectors where purity, reliability, and operational efficiency are critical.
Industries such as pharmaceuticals, food processing, semiconductor manufacturing, and chemical processing depend on dry vacuum pumps for their ability to handle demanding applications without the risks associated with oil-lubricated systems. The absence of oil reduces maintenance costs, minimises environmental impact, and enhances overall process safety.
The pharmaceutical industry requires precise, contamination-free environments for drug production, medical research, and packaging. Dry vacuum pumps support these operations by providing clean vacuum conditions, ensuring that no oil or vapours contaminate sensitive pharmaceutical processes.
Common applications include:
Dry vacuum pumps eliminate the risk of oil contamination, making them the preferred choice for high-purity pharmaceutical applications.
Food safety and hygiene regulations require strict contamination control in food processing and packaging facilities. Dry vacuum pumps provide the necessary vacuum conditions for food preservation without the risks of oil leaks or particle contamination.
Key applications include:
By using oil-free vacuum technology, food processors can maintain hygiene standards while improving operational efficiency.
Semiconductor fabrication and electronics manufacturing require ultra-clean environments where even microscopic contamination can affect product quality. Dry vacuum pumps provide the contamination-free vacuum conditions necessary for producing microchips, LEDs, and other high-tech components.
Applications include:
By eliminating oil contamination risks, dry vacuum pumps help maintain the stringent quality standards required in semiconductor and electronics manufacturing.
Chemical manufacturing involves handling corrosive gases, aggressive solvents, and volatile compounds that can degrade traditional vacuum systems. Dry vacuum pumps are built to withstand these harsh environments, providing reliable performance with minimal maintenance.
Common uses include:
Dry vacuum pumps are preferred in chemical plants due to their durability, resistance to harsh chemicals, and ability to operate without oil contamination.
Vacuum technology plays a vital role in aerospace and defence industries, particularly in testing, material development, and space simulation. Dry vacuum pumps ensure that these processes are conducted without the risk of contamination or performance degradation.
Key applications include:
Dry vacuum pumps provide the necessary precision and reliability for aerospace applications where accuracy is critical.
Vacuum technology is widely used in automotive manufacturing for tasks ranging from component testing to fuel system production. Dry vacuum pumps help achieve higher efficiency, reduced emissions, and improved quality control in the automotive sector.
Common applications include:
As the automotive industry moves towards electric and hybrid vehicles, dry vacuum pumps play a crucial role in producing advanced battery technology and precision-engineered components.
The energy sector, including renewable energy production and environmental protection, relies on vacuum pumps for various applications. Dry vacuum pumps provide a clean and efficient solution for gas capture, air treatment, and waste processing.
Common uses include:
By using dry vacuum pumps, environmental and energy companies can enhance efficiency while meeting sustainability goals.
Industries across the board choose dry vacuum pumps for their unique advantages, including:
Choosing the right dry vacuum pump depends on several factors, including:
Stanpumps offers a range of dry vacuum pump solutions, including:
The adoption of dry vacuum pump technology continues to expand across industries seeking clean, efficient, and low-maintenance vacuum solutions. Whether in pharmaceuticals, food processing, electronics, or automotive manufacturing, these pumps play a vital role in enhancing operational efficiency and product quality.
Industries worldwide trust Stanpumps' dry vacuum pump technology for its oil-free operation, energy efficiency, and low maintenance design. From pharmaceuticals and food processing to semiconductor and chemical manufacturing, our high-performance dry vacuum pumps ensure contamination-free, reliable, and cost-effective vacuum solutions.
Contact Stanpumps today to explore our advanced vacuum pump range and find the perfect solution for your industry. Let’s optimise your processes with clean, efficient, and sustainable vacuum technology!